Negli anni '40, le prime Jaguar XK120 utilizzavano pannelli di alluminio, mentre le auto da corsa C-Type e D-Type, che hanno dominato Le Mans negli anni '50, e la leggera E-Type degli anni '60 sono state all'avanguardia nella progettazione di chassis e carrozzeria in alluminio. Nel 2003 abbiamo riprogettato la nostra iconica XJ con una struttura dotata di pannelli e rivetti in alluminio che era del 40% più leggera rispetto a quella del modello precedente. Oggi le berline, le auto sportive e i SUV Jaguar possono contare su un'esperienza in fatto di alluminio maturata nel corso di cinque generazioni.
Il vantaggio principale dell'alluminio risiede nel suo peso, pari a un terzo di quello dell'acciaio. Questo ci offre la possibilità di creare chassis notevolmente più leggeri rispetto a quelli in acciaio, migliorando al contempo il consumo di carburante, riducendo le emissioni di CO2 e offrendo un'esperienza di guida più dinamica. Ogni 100 kg di peso risparmiati con uno chassis in alluminio contribuiscono a ridurre le emissioni di CO2 del veicolo di 9 g/km e migliorano il consumo di carburante fino a 800 litri nell'arco del suo ciclo di vita.
Ma la nostra filosofia in fatto di alluminio non è soltanto quella di risparmiare peso, ma anche di creare design più rigidi, sicuri, robusti e affidabili.
Siamo ormai esperti nell'uso dell'alluminio da impiegare nella produzione. I fogli di alluminio non lavorato, dello spessore di appena 0,9 mm per i pannelli esterni o fino a 3 mm nei punti in cui è richiesta maggiore robustezza, vengono stampati in forme complesse che conferiscono resistenza e, utilizzando una forza fino a 2.000 tonnellate, punzonati con precisione millimetrica. I risultati sono straordinari. Il pannello laterale di F‑PACE è uno dei più grandi che produciamo, ma nonostante questo ha un peso di soli 5,8 kg.
Traendo ispirazione dal settore aerospaziale, abbiamo sviluppato un metodo rivoluzionario per creare uno chassis in alluminio chiamato "riv-bonding". I pannelli di alluminio sono uniti fra loro da un adesivo ultraforte, quindi punzonati con rivetti in acciaio al boro zincati applicando una forza fino a 10 tonnellate.
Quando il telaio viene messo nei forni a 170 °C, l'adesivo si indurisce saldando in modo ermetico i due fogli di alluminio e trasformandoli in una struttura eccezionalmente rigida. Un esempio di questo metodo è la monoscocca in alluminio dell'auto sportiva F‑TYPE, che pesa solo 261 kg ma è dotata di una rigidità torsionale elevata. Con il modello XE, questa filosofia è stata portata a un livello superiore con la realizzazione della berlina Jaguar dal design con la maggiore rigidità di sempre.
La produzione di alluminio è un processo più silenzioso, pulito e che richiede minore energia rispetto alla costruzione di un tradizionale chassis in acciaio; inoltre, l'alluminio riciclato consuma appena il 5% dell'energia necessaria per la creazione di alluminio non lavorato senza compromettere l'integrità strutturale del materiale. Tutto ciò contribuisce a ridurre l'impatto ambientale di una Jaguar prima ancora che si trovi sulle strade.
La filosofia relativa all'alluminio non viene applicata soltanto alla produzione di uno chassis Jaguar più leggero, che offre prestazioni più efficienti e dinamiche e una maggiore resistenza e affidabilità. La nuova generazione di motori Ingenium Jaguar Land Rover utilizza un blocco di alluminio pressofuso che è più leggero di 24 kg, più efficiente in termini di attrito del 17% e più silenzioso di cinque decibel.
Per cui, i nostri nuovi veicoli sono più sicuri, più efficienti e più affidabili sotto ogni punto di vista.
ALTRE STORIE
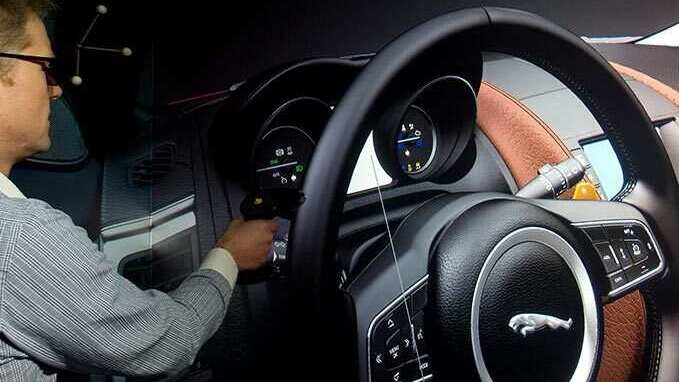
INGEGNERIA VIRTUALE
Stiamo effettuando investimenti importanti in strumenti di ingegneria virtuale all'avanguardia che consentano la progettazione più rapida, efficiente e solida dei nuovi prodotti e delle tecnologie avanzate che ne sono alla base. Ciò offrirà alle auto Jaguar maggiori livelli di affidabilità, resistenza e sicurezza.
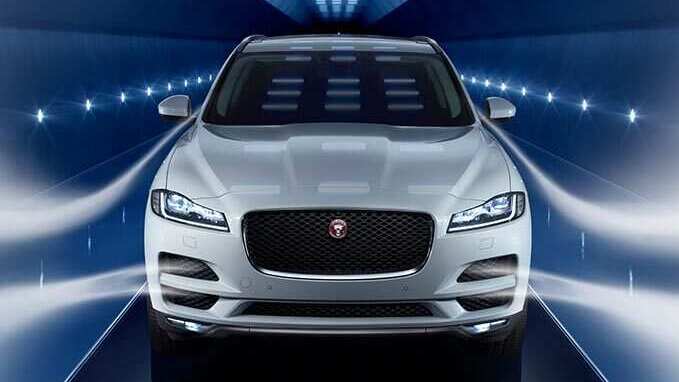
PROCESSO DI TEST
In ogni fase della progettazione, dello sviluppo e della produzione, ogni componente di una Jaguar viene sottoposto a migliaia di test e controlli per verificarne la sicurezza, la resistenza e la qualità, garantendo che il prodotto finito sia l'auto più affidabile, resistente e sicura che si possa guidare.